Why even defect prevention isn't enough
"Just because nothing is wrong, doesn't mean anything is right."
This post was first published on the agile Teams WordPress blog on May 12, 2009. As of July 12, 2024, all agile Teams content has moved here to Agile Analytics and Beyond. Minor edits have been made to support audio voiceover for the podcast.
During a recent stay at a reasonably nice hotel, I was looking for a place to hang up my wet raincoat when I noticed this sign on the wall, up high. (The sign has a picture of a clothes hanger with a red slash through it, right below the sprinkler head protruding from the wall.)
Clearly there had been problems in the past with sprinkler malfunctions, and after one or more incidents of 'defect correction' (fixing the sprinkler malfunctions), someone did root cause analysis (e.g. why? ... why? ...), identified coat hangers as the culprit, and took this action to try to prevent future defects.
Commendable, right?
But I looked around the entire hotel room and realized I still had no good place to hang my wet raincoat.
This exemplifies a saying I recall hearing in a SEI Six Sigma training class last year, and earlier in a QFD class: Â Â Â Â
"Just because nothing is wrong, doesn't mean anything is right."
Taking corrective and preventive actions, and driving defect levels towards zero, may be useful and necessary, but is not sufficient to achieve true high quality. Satisfaction of real customer needs matters most.
It would be neither hard nor expensive to install a coat hook somewhere in the hotel room for wet/snowy/dirty/... outer garments. Adding this small amenity would dilute the temptation to guests who might otherwise hang wet coats on the sprinklers. And they'd be less likely to drape them over the chairs in the rooms, which probably isn't good for the wood or upholstery.
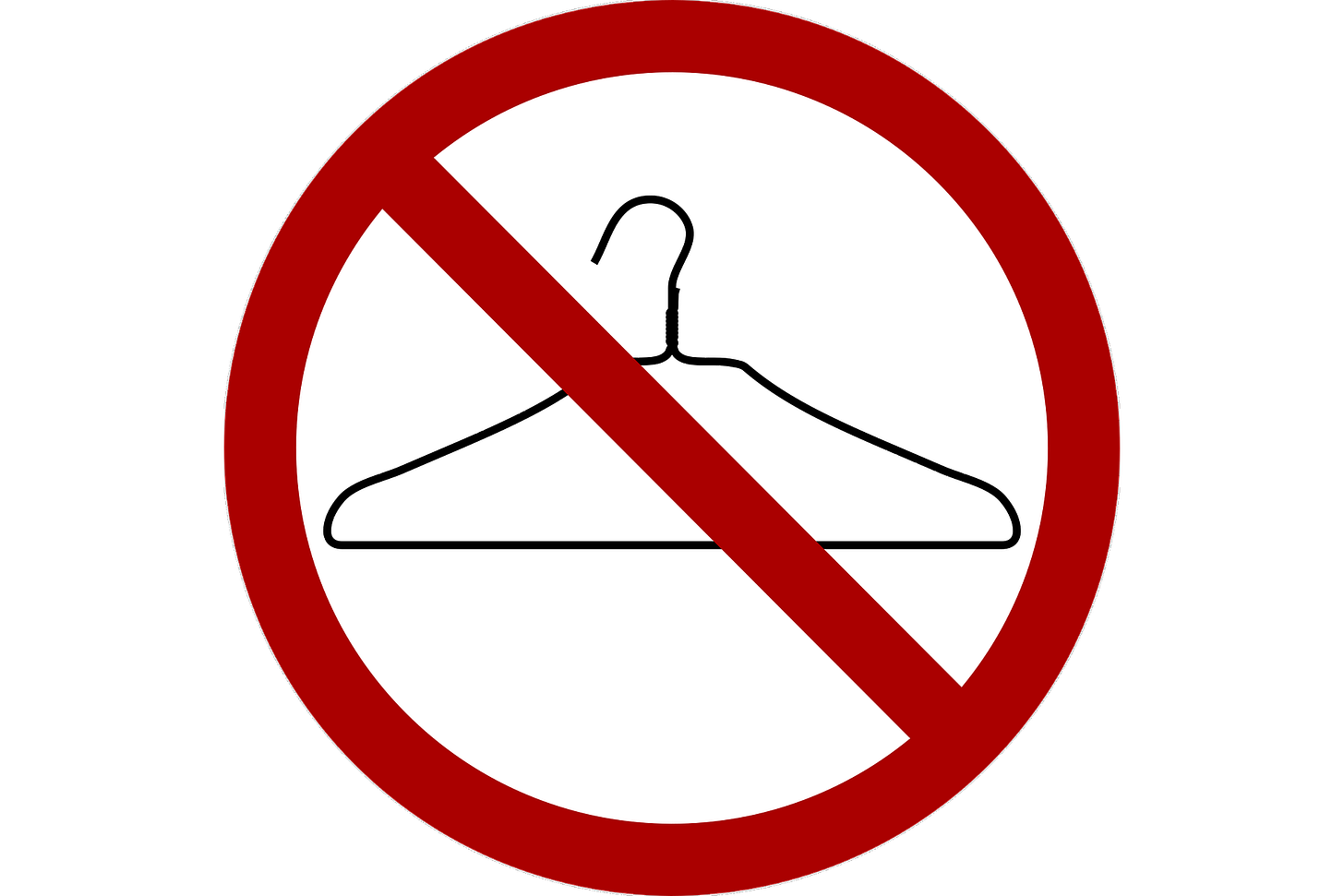